News
トータルピッキングとは?特徴やメリット、デメリットをご紹介
ピッキングとは
トータルピッキングの説明をする前に、そもそもピッキングとは何か、どんな種類があるかについてお伝えしようと思います。
ピッキングは、指示された商品を保管棚からピックアップして、指定された別の場所へ集めることです。たくさんの作業スタッフが広い倉庫内の棚と梱包エリアを往復しながら集めて回るピッキング作業は、物流倉庫内作業の中で最も負荷がかかる工程ではないでしょうか。ボトルネックになりがちなピッキング工程ですが、作業方法によって大幅に作業効率を改善できる工程でもあります。
今回はピッキングの種類とトータルピッキングのメリット・デメリット、そしてデメリットをどのように補うかについても詳しく説明したいと思います。
ピッキングの種類
ピッキングには大きく分けて「シングルオーダーピッキング」と「トータルピッキング」「マルチオーダーピッキング」の3つの方法があり、それぞれ別の呼び方があるため、呼び方も含めて解説していきたいと思います。
■ シングルオーダーピッキングとは
「シングルオーダーピッキング」とは、1オーダー(受注)単位で商品をピッキングする基本的なピッキング方式で、それ以上仕分けが出来ない単位でもあります。別名として、「シングルピッキング※」「オーダーピッキング※」「摘み取り方式」があります。
例えば、単行単品、1商品1品1オーダーごとにピッキングしていくことのみを指して「シングルピッキング」と呼ぶ場合があります。混同を避けるために、本コラムでは複数の商品があっても1オーダーごとにピッキングすることを「シングルオーダーピッキング」と表記いたします。また、「シングルピッキング」と「オーダーピッキング」を違う意味で分けて使う場合稀にあります、たとえば、1オーダーで同じ届先でも、午前と午後など時間別に配送する場合には、「シングルピッキング」ではなく、「オーダーピッキング」であるという定義で運用される場合です。ただ、一般的には「シングルピッキング」と「オーダーピッキング」は同じ意味で運用されている場合が多いです。
最もシンプルなピッキング方法ですが、100オーダーあれば保管棚と出荷エリアを100往復する必要があるため、総出荷数が少ない場合や、出荷オーダーの組み合わせの際に個別対応が必要な場合などに適しています。
トータルピッキングとは?
「トータルピッキング(トータルピック)」とは出荷オーダーの総量をまとめてピッキングし、その後工程として、出荷オーダー別に仕分けをする方法です。どこまでをまとめてピッキングしてくるかは、後工程の間口数によって変わってきます。例えば、30間口のGASが後工程にある場合には、30オーダー分をトータルピックして持ってきます。いったん集めた商品を、発送先毎に振り分けるため「種まき方式」とも呼ばれます。別名「バッチピッキング(バッチピック)」、「総量ピッキング(総量ピック)」、「集約ピッキング(総量ピック)」とも呼ばれます。
■ マルチオーダーピッキングとは
広義の「マルチオーダーピッキング」は2つ以上の出荷オーダーをまとめてピッキングすることを言いますので、「トータルピッキング」も「マルチオーダーピッキング」の一つと考えることが出来ます。しかし、一般的には台車に複数のカゴを乗せてピッキング兼仕分けをする、マルチピッキングカートを用いたピッキング方式を指すことが多いです。
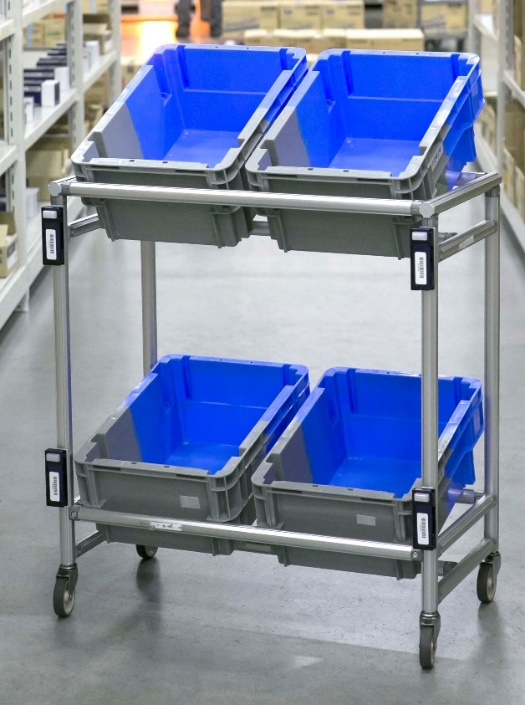
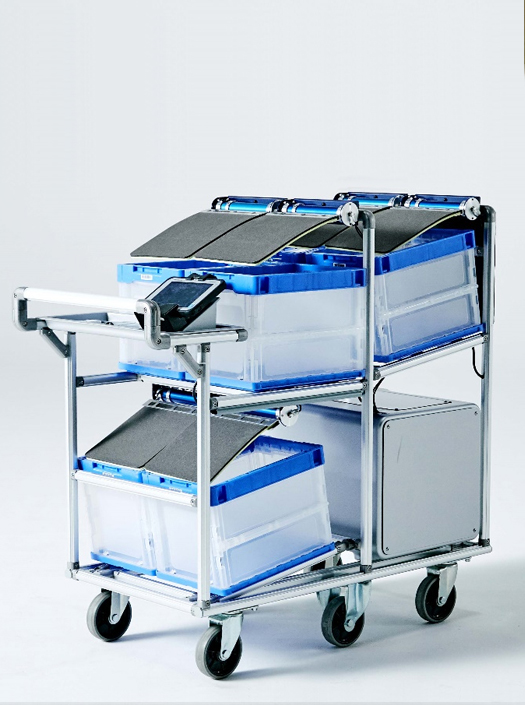
マルチオーダーピッキングは、シングルオーダーピッキングが1オーダーごとにピッキングしてくるのに対して、複数を同時にピッキングしてくることが出来るため、当然シングルオーダーピッキングよりも、歩行距離が減り効率が上がりますが、シングルオーダーピッキングの場合は、ピッキングして台車に乗せた1つのカゴに間違わずに投入することが出来ますが、マルチオーダーピッキングの場合は複数のカゴがあるため、間違ったカゴに投入してしまうリスクがあります。上記写真のマルチピッキングカートはそうした誤投入を防ぐために、STOCカートには、各カゴ付近にSTOC(ボタン電池駆動無線 LEDタグ)がついており、ピッキングした商品をスキャンすると、STOCが光って投入するカゴを知らせてくれる仕組みです。さらにG-CARTにはそれぞれのカゴにゲートがついており、該当する箇所のみが開くため誤投入を完全に防ぐことが出来る仕組みになっています。
トータルピッキングの特徴
「シングルオーダーピッキング」「トータルピッキング」「マルチオーダーピッキング」とピッキングの種類について説明いたしましたが、ピッキング効率化のカギとなる「トータルピッキング」について掘り下げていきましょう。
上の図をご覧ください。シングルオーダーピッキングする場合とトータルピッキングする場合を比較し て見ていきましょう。シングルオーダーピッキングは1オーダーごとに毎回往復するため、3往復する のに比べ、トータルピッキングでは1往復でピッキングが完了します。またシングルオーダーピッキン グでは、違うオーダーに同じ商品が含まれていた場合でも、オーダーごとに商品をピッキングするた め、ピッキング箇所の合計は 8 か所になり、トータルピッキングの場合、重複した商品をまとめてピッ キングできるため、ピッキング箇所は4か所になりました。
このようにトータルピッキングはシングルオーダーピッキングと比べて往復数、棚に立ち寄る回数を減らすことで、歩行距離を減らすことが出来ますが、トータルピッキングした後には必ず、オーダーごとの仕分け作業が必要になります。トータルピッキングによって生産性を上げるためには、この仕分け作業を速く正確に行うことが重要になります。
この説明では便宜上3オーダーを集約してピッキングしていますが、実際の運用では例えば30間口あるゲート・アソート・システム(GAS:ガス)で仕分けを行う場合には、1バッチである30オーダーをトータルピッキングしてくることになります。当然一度にたくさんのオーダーをまとめてピッキング出来ればさらに効率が上がります。
トータルピッキングのメリット
トータルピッキングの概要について説明させていただきましたが、改めてメリット・デメリットという切り口で整理していきましょう。
■ ピッキングの際に、作業スタッフが商品を探す時間、移動距離、移動時間を短縮
物流センター内での作業員の移動距離・時間を効率化できる点が最大のメリットです。多数の作業員がいっせいに近場のロケーションに殺到し、単独出荷先の商品をピッキングするより、はるかに効率化できます。作業導線が大幅に減少し、作業効率が格段に向上します。
トータルピッキングのデメリット
■ 作業工程が増える
トータルピッキングした後工程として、出荷オーダー別の仕分けが必要になるため、シングルオーダーピッキングと比べると「仕分け」の1工程が増えることになります。そのため、作業工程が増えるだけでなく、ピッキングと仕分けそれぞれ工程で、ミスが起きてしまう可能性が出てきてしまいます。トータルピッキングの最大のデメリットはこの「仕分け」工程が増えてしまうことです。
■ 仕分け作業用の場所が必要になります。
まとまった数に対応できる仕分け作業用の場所を確保する必要があります。人手ではなくピース仕分けソーター等を使えば、素早く正確に仕分け出来ますが、設置面積は広大で導入コストも安価ではありません。
■ SKU数が多い時に、ピッキングエリアが広範囲になってしまう。
SKU数(stock keeping unit=最小管理単位)が多いと、広範囲に点在するアイテムをピッキングする必要が出てくるため、運用の仕方によっては歩行距離の削減があまり出来ない場合があります。
トータルピッキングの生産性を最大化するには
ピッキングを効率化するためのトータルピッキングですが、前項のようなデメリットがありますので、トータルピッキングの生産性を最大化するためには、このデメリットを最小化する必要があります。
■ 作業工程を増やさない
トータルピッキングの最大のデメリットは、「仕分け」の工程が増えてしまうことでした。このデメリットを無くすためには、検品を兼ねて仕分けることが出来る※GASを使うことで、シングルオーダーピッキングと比べて工数が増えるというデメリットを無くすことが出来ます。
※ GAS:ガス、ゲートアソートシステム。各間口にゲート(ふた)を設け、商品のバーコードをスキャンすると、該当する間口のゲートだけが開き、そこに商品を投入する。開いたゲートにしか商品を投入できないので、入れ間違いは物理的に起こらず、仕分け後に従来行っていた検品をする必要が無い。もちろん、ゲートが開くことで投入箇所も明確なため、仕分けのスピードも大幅に向上する。
■ 仕分け作業の仕様面積を最小化する
使用する床面積もコストになるため、仕分け作業に使用する面積についても狭い方が良いわけです。前述の通り、ピース仕分けソーターは早く正確に仕分け出来ますが、大がかりな設置面積が必要になってしまいます。こうした場合もGASを使用することで、早く正確に仕分けが可能で、同じ能力の場合、ソーターの半分程度の面積で設置することが可能です。
■ SKU数が多くても、歩行距離を最小化する。
SKU数が多い場合に、広範囲に点在するアイテムをピッキングする必要が出てくるため、歩行距離の削減があまり出来ない場合があると前述しましたが、これを防ぐための方法として
・ローケーション改善
アイテムごとの出荷頻度を見ながら、商品をどの棚に保管すると歩行距離を削減できるかを考えて、ロケーションを改善する。
・ゾーンピッキング
保管棚のゾーンごとにバッチ(オーダーの取りまとめ)を分けてピッキングすることで、作業者の歩行距離を削減し、作業の効率化が図れる。
・LSS(ロジスティック・スマート・システム)
タクテックのピッキング効率化のためのソリューション。トータルピッキングをする際に、歩行距離を最小化するためにバッチ(オーダーの取りまとめ)を組み直し、出来たバッチの中で更に歩行距離を最小化するためにピッキングルート(ピッキングする順番)を最適化する仕組み。
まとめ
少し宣伝も入ってしまいましたが、ピッキングについて網羅的に見ながらトータルピッキングについて説明いたしました。デメリットさえ抑えれば、トータルピッキングが万能のような書き方をしていますが、例えば、大きくて重い商品が多い場合、まとめてオーダーを取ってくるトータルピッキングを行うことは不可能です。最適なピッキング方法を考える上では、あくまでも実際の商品や出荷数、SKU数などの様々な条件の中でシミュレーションをしていく必要があります。
お話をお伺いしてシミュレーションを行いピッキングの効率化の提案をさせていただきますので、タクテックにお気軽にお声がけください。